Ajit Panicker, Founder and CEO of Pureblu Technologies Pvt. Ltd., notes that India’s unprecedented demand for air conditioners necessitates focusing on a skilled workforce and adopting energy-efficient technologies to ensure sustainable growth and optimal performance.
The demand for cooling systems, especially air conditioners, surged to unprecedented heights, and mercury steadily climbed across India. What was once considered a luxury has become an essential commodity for millions, driven by population growth and rising disposable incomes.
According to projections by the International Energy Agency (IEA), the proliferation of air conditioners is poised to skyrocket, with expectations of a nine-fold increase by 2050. This trajectory suggests that by 2050, one billion AC units will be across Indian households.
However, this surge in demand brings numerous challenges, ranging from manufacturing- cost optimisation to meeting the energy-efficiency & green refrigerant standards. Additionally, ensuring proper installation and maintenance practices is crucial to safeguard the longevity and safety of households.
Shortage of skilled workforce
One of the most pressing challenges facing the Indian air conditioning industry is the acute shortage of skilled workforce. Despite the promising growth prospects, government initiatives for technician skilling are scant, and certifications still need to be available. This gap results in inconsistencies in installing air conditioners and compromises in performance, safety and quality, with many technicians relying solely on on-the-job training.
Moreover, the gig economy’s emphasis on quick fixes undermines the development of technical skills. However, this sector does not contribute to skill development among workers. Moreover, as this segment becomes increasingly saturated with workers, individuals employed in it may eventually find themselves needing employment or valuable skills.
Due to their scale of operations and limited personnel needs, micro, Small, and Medium Enterprises (MSMEs) in the sector often prioritise short-term benefits over long-term personnel development. Inadequate compensation for service partners leads to shortcuts and compromises artistry, further exacerbated the problem.
Certification and quality challenges in AC manufacturing
Mandatory certifications for technicians can ensure a baseline competency level, providing consumers with assurance regarding service quality. Industry partnerships can incentivise upskilling and specialisation among technicians, helping grow a culture of continuous learning. Educational institutions can play a vital role by offering HVAC&R courses and industry internships. This will create a pipeline of skilled professionals to meet the industry’s growing demands.
The second challenge OEMs face is optimising the cost of production of ACs to meet the improved energy-efficient norms and shift to green refrigerants. The OEMs use alternative and cheaper materials to ensure that manufacturing costs remain unaffected. However, this pursuit often needs to improve the quality of materials employed in AC manufacturing. A prime example of this compromise is the adoption of aluminium alloys or PFCs heat exchangers, which were prevalent in the early 2010s. However, these heat exchangers faced several issues related to leakages and corrosion.
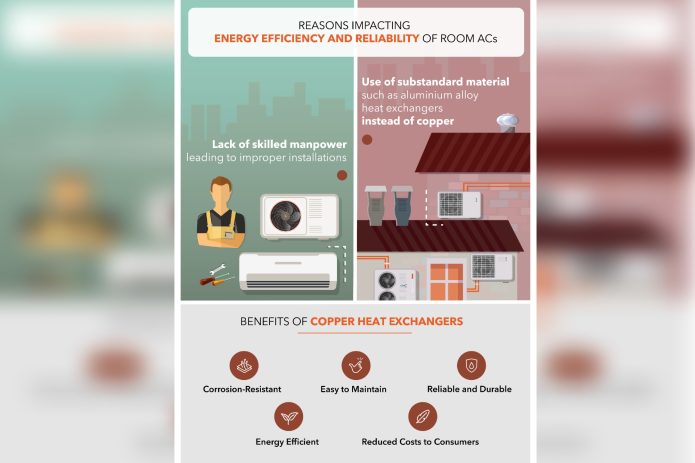
The concurrent issues of substandard materials and shoddy craftsmanship significantly hinder the functionality of AC units, directly affecting consumers. These faulty installations also undermine the Star Labelling system for ACs, causing them to operate below their designated Star Ratings. Consequently, energy efficiency drops, resulting in higher electricity bills for users.
As a result, OEMs returned to trusted copper heat exchangers, which have proven to be corrosion-resistant, easy to maintain, reliable, and durable. Furthermore, technological innovations in heat exchangers led to the adoption of smaller-diameter copper tube heat exchangers. This ensures the quality of the ACs and their adoption, and it is also an economical, eco-friendly, and energy-efficient solution.
In conclusion
Investing in technologies prioritising energy efficiency aligns with India’s climate goals. It also reduces operational costs for consumers. By prioritising energy-efficient cooling solutions, we lay the foundation for a cooler, more sustainable future for future generations. In conclusion, India’s AC boom presents a win-win opportunity for all stakeholders with a focus on a skilled workforce and copper-based, energy-efficient technologies.
Ref: (2023). Radial Thermoelectric Model for Stranded Transmission Line Conductors. Sensors, 23(22), 9205.
Cookie Consent
We use cookies to personalize your experience. By continuing to visit this website you agree to our Terms & Conditions, Privacy Policy and Cookie Policy.
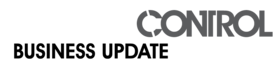